#2 数字化卓越运营
精益化、自动化、数字化转型
智能制造工厂建设和数字化转型的误区
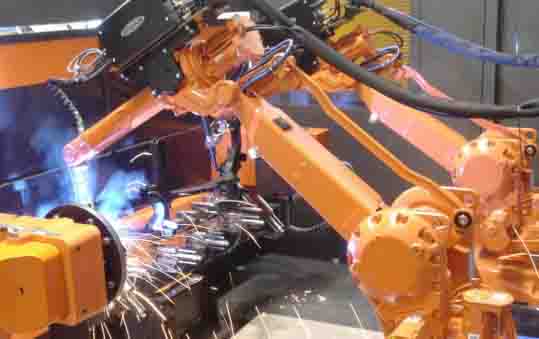
盲目引进自动化设备
企业没有对需求进行系统性分析,认为自动化设备或机器人就等于智能制造
采用单一的节省人工数量来衡量智能化
企业认为智能化就是要实现少人化、无人化,并从单台设备或单个系统模块的层面去评估哪部分值得投入,忽视了整体性,没有进行多维度、全方位评估
没有实现设备数字自动采集和联网
企业仍继续使用传统的设备,忽视了设备数据采集的重要性,数据没有采集或者仍旧是大量人工填写表单的方式;设备之间没有进行互联互通
运营管理基础薄弱,认为投资可以解决一切管理问题
企业没有做好精益管理,流程设置不合理,管理意识薄弱,管理能力缺乏。企业希望买一台自动化设备或者上个高级管理软件就可以解决这样的问题
通过三化融合实现数字化卓越运营
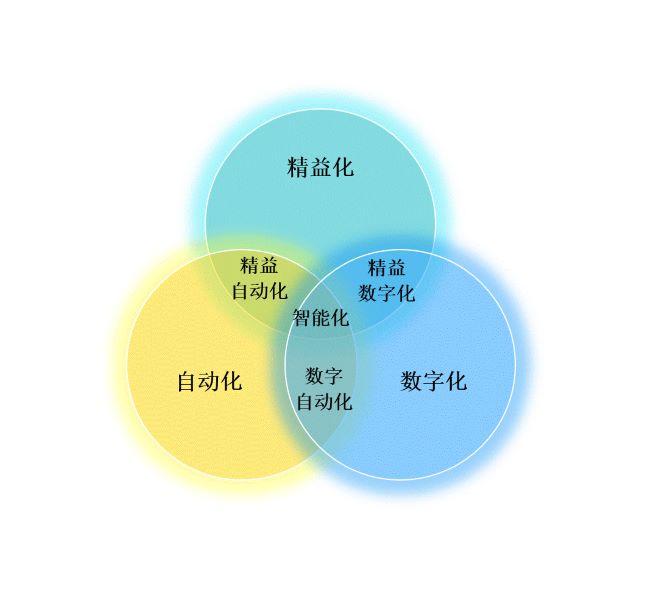
精益化的原则
- 精确定义客户价值,让员工致力于增值活动 Value
- 贯穿整个价值流的分析、改进、管理 Value Stream
- 尽可能建立连续流 Flow
- 采用拉动式生产 Pull
- 持续改进、追求完美 Perfect
自动化的原则
- 不要在不合理的生产流程上实现自动化
- 流程优化基础上再实现自动化,将防止不合理的流程固化和浪费的放大
- 优先针对重复性高、危险性高、操作困难的作业(3D岗位)进行自动化
数字化的原则
- 业务管控:通过信息化技术让管理流程标准化和落地,实现管理透明化,数字化
- 工具赋能:通过信息化,让人员摆脱重复的事务性工作,专注业务提升,实现信息流动自动化
- 价值积累,辅助决策:通过信息化,快速建模,快速数据分析,快速得到决策依据
数字化卓越运营方面的咨询服务
生产与物流优化
精益生产与精益物流
产能、效率、质量、交货期、成本等绩效提升,如:
- 5S、可视化管理、车间现场管理(SFM)
- 车间布局设计与优化
- 生产线和工位设计、流动生产、JIT
- 拉动系统建立PULL,内部物流优化
- 仓储设计和布局规划
- 生产计划优化及库存管理
- 全员设备维护(TPM)
- 设备快速换型(SMED)
- 安灯系统与自働化 Andon & Jidoka
自动化评估及设计
基于操作层级的全流程自动化机会识别和设计:
- 生产自动化
- 物流自动化(智能仓储、智能物流)
- 检验自动化
- 低成本自动化设计(LCA)
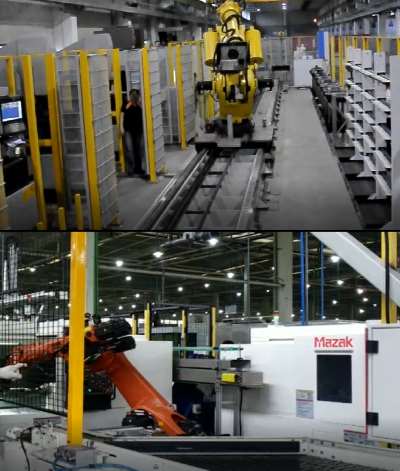
制造数字化
制造数字化评估
- 数字化成熟度评估、智能制造能力成熟度模型
- 改进建议及推行路线规划
制造信息化系统规划和优化
根据新的业务模式,规划业务流程、关键数据、网络等,如:MES系统、APS系统、SCADA系统
数字化现场管理
在现场采用数字化技术和工具,使现场透明化,提升管理效率,如:数字化报表、数字化安灯系统及问题追踪、数字化防错系统、数字化TPM等
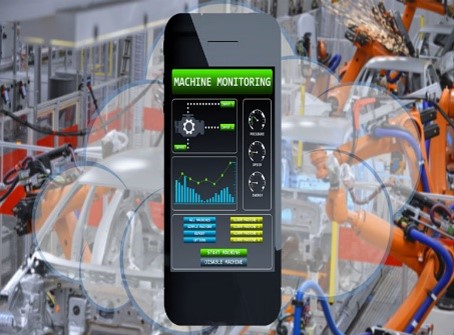
精益导入&转型
精益评估
采取多种方式(如价值流诊断、精益成熟度评估)等对企业在精益战略、精益推行方法、精益推行成效等方面进行评估,并对企业未来的生产方式、精益推行路线进行规划
企业精益体系搭建
对标精益标杆企业的生产体系,结合企业自身特点,设计企业精益体系XPS/XBS
精益变革管理和精益转型项目辅导
- 精益培训(精益理念、精益方法、精益工具等)
- 精益试点项目辅导(精益生产、精益物流、精益行政/精益服务/精益办公等)
- 精益管理(精益战略、精益组织、精益活动等)
- 精益人才选拔和培养、KATA Coaching
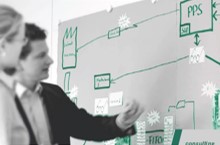
组织与文化建设
精益行政、精益办公、精益研发
- 非生产领域的精益推行、流程优化
战略部署与业绩管理
- 战略部署:基于愿景、使命和策略的目标和任务定义
- 辅导KPI分解及建立跟踪体系,例如层级会议
组织搭建和领导力
- 帮助进行精益化数字化组织架构设计,工作流程梳理、岗位描述设定
- 定义不同层级的精益化数字化活动,如CIP小组、合理化建议流程
- 明确管理层在变革中的角色和任务
人才及领导力发展
- 理论培训、项目实践相结合的方式,进行基础培训、专家培养
- 知识体系的搭建
- 内部专家评估认证体系的搭建
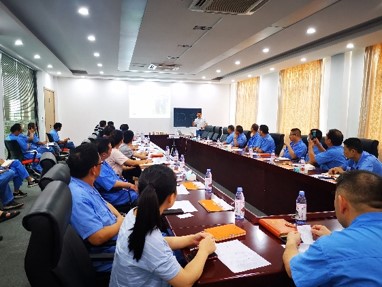